Bosphorus Strait Trans-strait Railway Construction Project
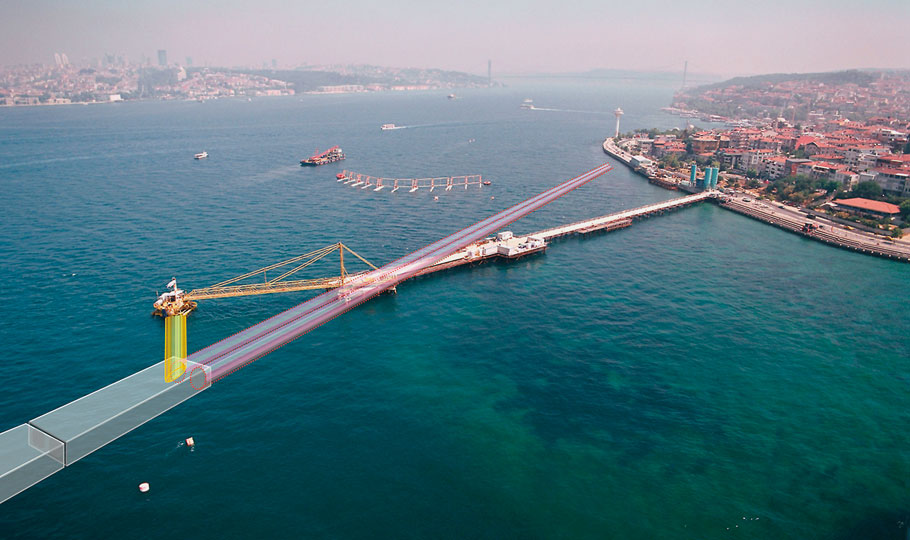
The Project to Construct a Bosphorus Strait Trans-strait Railway was an infrastructure outfitting project undertaken in 2004 with Japan's Official Development Assistance in the Republic of Turkey (hereinafter: Turkey) to construct an approximately 13.6km trans-strait railway crossing the Bosphorus Strait and its approach tunnel as well as 4 station buildings. Construction was advanced using both the submerged tunnel method for the part crossing the Bosphorus Strait, with its high tidal speed, and the shield method and NATM (New Australia Tunnel Method) for the land tunnel part. It received great praise not only in Turkey and Japan but from around the world for its accomplishment of very technically difficulty construction, such as achieving the direct junction of a shield tunnel and submerged tunnel below the seabed, which was a world first.
The Japan Society of Civil Engineers takes up the Project to Construct a Bosphorus Strait Trans-strait Railway, because
- 1)The submerged tunnel was constructed at a water depth of 60m, which was the deepest construction in the world.
- 2)The implementation of the submerged tunnel method in the Bosphorus Strait, which is crossed by a great number of ships, was undertaken under extremely harsh construction conditions of a surface velocity of up to 3m/s and differing flows on the surface and underneath.
- 3)At the time of the submerged tunnel construction, a reduction of the construction time by one year and construction costs by 10% were realized compared to traditional methods by using construction methods without departure shafts and arrival shafts from the conditions of the surrounding geological features.
- 4)Shield tunnel and submerged culverts were directly joined without using arrival shafts under the Bosphorus Strait for the first time in the world.
- 5)Japanese engineers gave effective technical transfer to the local construction counterparts effectively through all day training.
1Project Background
The Bosphorus Strait trans-strait railway is a seabed railway connecting the Asian side and the European side of Istanbul (see Figure 1). Istanbul is split between Asia in the East and Europe in the West by the Bosphorus Strait, and the means to cross the strait were limited to ferries and 2 suspension bridges. Over 90% of the passenger transit in the city being on the roads causes chronic traffic congestion and air pollution. And so by constructing the seabed railway, it responded to the traffic demand while also playing the vital role of promoting the reduction of air pollution and the optimization of socio-economic activities.
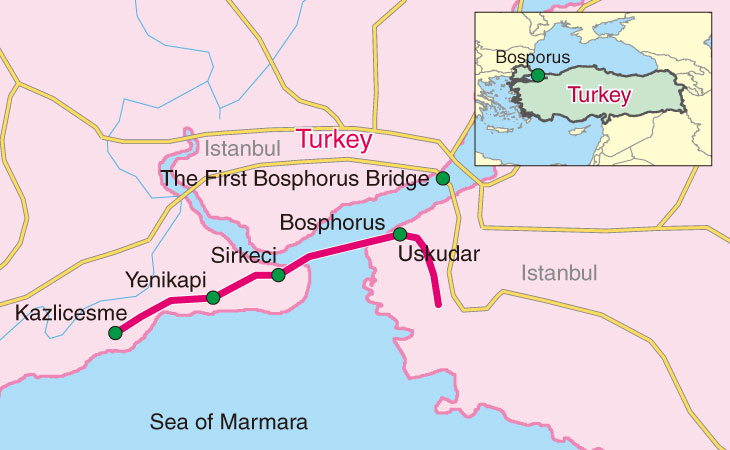
2Project Chronology
2.1Project Formation Stage
1970s | Connect the strait part with the seabed tunnel and incorporate a plan to run a commuter train through it into the urban transport master plan. |
---|---|
Start of 1980s | Feasibility study and outline design are implemented mainly by western consultants. |
1998 | Turkish government officially requested yen loan program to the Japanese government. |
The idea to connect the Asian side and the European side had already been conceived by engineers in the 1860s who envisioned a plan to run a steam locomotive through a pipe submerged to the bottom of the sea (see Figure 2). However, the tunnel construction was not implemented due to technological difficulty, and for crossing the strait, 2 suspension bridges including the No. 2 Bosphorus Bridge, which was constructed with yen loan program and ferries, were used.
Over a long time, in order to resolve the traffic issues in the Bosphorus Strait in the 1970s, the Turkish government incorporated a plan to connect the traffic networks separated by the strait and run high density commuter trains into their urban transport master plan. In the 1980s, feasibility study and outline designs were implemented mainly by western consultants, and although the construction of a trans-strait railway would be technologically difficult, however, it was shown to be feasible. Some international cartels that showed interest in this project started moving to approach the Turkish government presuming the use of BOT (Build Operate Transfer), but due to financial issues, etc., it never made it to implementation. The Turkish government subsequently highly evaluated Japan's technology, and in 1998 under partially untied conditions, they officially requested yen loan program to the Japanese government.
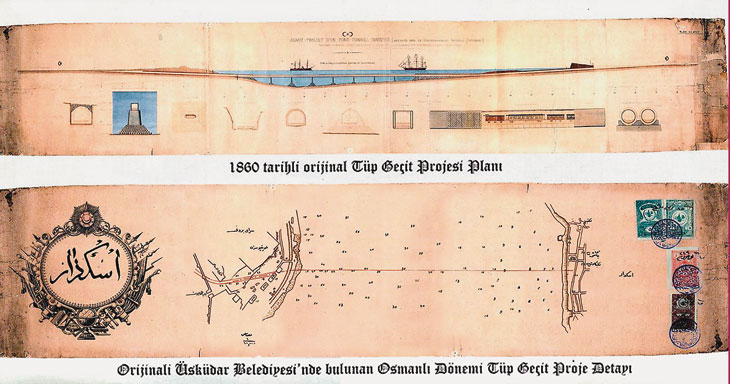
2.2Project Execution Phase
Sep. 1999 | 1st stage international yen loan agreement is executed (approximately 12.5 billion yen) |
---|---|
2001 | Selection of consultants made |
2004 | Contractors (joint venture represented by Taisei Corporation) to execute the construction of the strait part and the 4 stations are selected |
Feb. 2005 | 2nd stage yen loan agreement is executed (approximately 98.7 billion yen) |
Jan. 2010 | Additional yen loan agreement is executed (approximately 42.1 billion yen) (due to delay of construction caused by excavation of historic ruins) |
Oct. 2013 | Opening ceremony is held on the 90th anniversary of the founding of Turkey |
Having received the application from the Turkish government, Japan Bank for International Cooperation (presently JICA) negotiated with the Turkish government regarding the necessity, technical feasibility, funding plan, etc., of the project and drew it up. As a result, in 1999 an agreement for 12.5 billion yen was executed as the 1st stage yen loan. Taking into account the environmental improvement effect of reducing the air pollution, which was one of the purposes of this project, the Japanese government granted it as a special environmental yen loan with low interest.
Because the project was extremely technologically difficult, it was agreed that the construction of the main structure would be partially untied, and the consultants would be bilateral tied. The consultant selection, which was conducted in 2001 the bid of a joint venture represented by Pacific Consultants Co., Ltd., was accepted, and subsequently in 2004 international competitive bidding was conducted to select contractors for the Bosphorus Crossing, to construct a 13.6km extension between the Bosphorus Strait as well as the 4 stations. As a result, a joint venture represented by Taisei Corporation was selected and a group of Japanese companies was lined up to handle the future of this project.
The construction was started in August of 2004, and in February 2005 an agreement for 98.7 billion yen was executed as the 2nd stage yen loan. However, because it was more difficult than predicted due to the survey of historic ruins on the land for the station buildings, construction delays began from around mid-2005, due to the survey of historic ruins. Frequent discussions were held on the owner and contractor sides regarding the responsibility for these delays, resulting in the acknowledgement that "the responsibility for the survey completion delay which affected the schedule before and during construction lies with the owner", and in January 2010 a changed agreement for extended construction and additional funds was established based upon this acknowledgement.
Construction subsequently proceeded and a ceremony celebrating the partial opening was held on October 29, 2013 to coincide with the 90th anniversary of the founding of Turkey. Prime minister Shinzo Abe attended from Japan, and he gave words of commendation to all the related parties who had accomplished the difficult construction while emphasizing the strong partnership between the two countries, including Taisei Corporation.
3Project Features
3.1Submersion of Submerged Culverts to a Depth of 60m for the First Time in the World
As a technique to cross the Bosphorus Strait, the owner side designated the submerged tunnel method, but it was the first attempt at a depth of 60m in the world.
The flow velocity in the Bosphorus Strait from the Black Sea side is usually 1-2m/s (maximum velocity of 3m/s) in the surface level, and underneath there is a flow (1m/s) in the opposite direction, causing a complex tidal current. Furthermore, there are no regular "tidal stops" caused by the tide in the Bosphorus Strait, and changes in wind and air pressure cause sudden changes of 2m/s and higher in the surface level every few hours, making an extremely harsh environment to implement the submerged tunnel method.
To combat these restrictions, Japanese engineers had compiled precise data including water level, flow velocity, wind direction and speed, and air pressure from more than one year before the start of construction to work up a plan to be able to avoid the high flow velocities in when submerging. Furthermore, based upon this data they newly developed an "Information Communication Technology (ICT)" which estimates future flow condition changes in a few minutes. Also, the submerged culverts were guided to the sea bottom using positioning combining GPS rotating multi-beam echo sounders, gyro-compasses, and angle meters, and in the final stage when the submerged culverts were joined, a "Submersion System" was developed to measure and control with high precision ultrasonic measurement equipment. Through these systems, the submersion of all the submerged culverts was completed within the planned period, and it was accomplished within the precise limited range (within 8cm) for installing the submerged culverts.
An issue which differs from the tidal currents is that because the shallow sea terrain is spread out in the bedrock on the bank of the Bosphorus Strait, the construction of departure shafts, which are generally necessary in constructing submerged tunnels, would require a great deal of time and funding. As a means to resolve this issue, Japanese engineers proposed constructing a submerged tunnel in the offshore section 350m from the bank on the Asian side and 200m from the bank on the European side and connecting the submerged tunnel edges on both sides with a shield tunnel underwater. Also, fitting with this construction method, after the initial submersion of the submerged culverts they installed temporary shafts (access shafts) directly upon the submerged culverts to secure an access route into the submerged tunnel culverts (see Figure 3). Through this construction method of not using departure or arrival shafts, a reduction of the construction period by one year and construction costs by 10% were realized, compared to traditional methods.
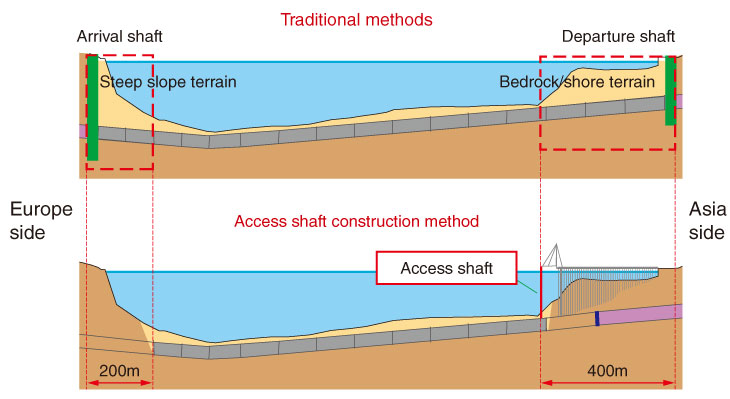
3.2Schemes in the Shield Tunnel Construction Method to Combat the Rapidly Changing Bedrock
The same as the submerged tunnel method, it was designated by the owner side to use the shield tunnel construction method for the tunnel parts outside the Bosphorus Strait as well. Also, at a depth of 60m and being the place where the submerged culverts were backfilled, the work had to be done under extremely high pressure. And so in order to handle the places with the most severe conditions, an airtight muddy water type shield method was adopted. In the general shield tunnel construction method, excavation is conducted while exchanging/inspecting the bit (a disc-shaped disc cutter) on the front surface, but in this project an airtight type was adopted. Furthermore, everything other than the joined part was hard bedrock, so there was no option but to construct a long distance (approximately 14.6km) bedrock via an airtight shield tunnel construction method. Such a long distance bedrock being constructed via an airtight shield tunnel construction method is a rare experience even in Japan.
Also, because Turkey is an earthquake-prone country, igneous rock has penetrated into the sedimentary rock, and the surrounding area has been subject to thermal metamorphism and pressure metamorphism by magma and become clay and boulders. Therefore, places where hard layers and soft layers appeared alternatingly and places where the granularity was different from the bedrock with a great deal of boulders, clay, and crevices were seen every 50-60m, where short, and even every 200m, where long. In the muddy water type shield method, in order to maintain a fixed pressure, it is necessary to excavate while changing the properties of the muddy water. As a result, the longer the distance, the more time it takes to change the properties of the muddy water and send it to the edges. Additionally, in the bedrock with many crevices, the crushed bodies are larger than expected, and so they get stuck in the pipe when sending them to the bank, creating the risk of blockage, sudden rises in pressure, and damage to the equipment.
And so the following improvements were implemented, improving the excavation speed.
1) Remodeling of cutter face
Because wear on the external disc cutter is especially rapid, the intake openings and external disc cutters were expanded and increased in size.
2) Improvement of fluid equipment
In order to prevent blockage and reduce the removed earth load, 2 rotary crusher units were serially installed where there was 1 unit originally, and the size of the crushed bodies of removed earth were made reliably smaller.
3) Improvement of muddy water processing equipment.
In fitting with the mud removal capacity, the muddy water processing capacity was also improved.
4) Reinforcement of personnel
The efficient exchange of parts, etc., was implemented by organizing a maintenance group with experienced Japanese supervisors to conduct regular inspections and periodic maintenance.
3.3Direct Junction of Shield Tunnel and Submerged Tunnel at the Seabed for the First Time in the World
Regarding the adoption of the submerged culverts and shield tunnel construction method mentioned above, because it was a requirement on the owner side, it was necessary to join both construction methods at the seabed where there was pressure of 0.4MPa on the Asian side and 0.6MPa on the European side.
In order to safely execute the joining work, reliable water stoppage was required for this joining, so the Japanese engineers had repeated discussions and examinations regarding this and decided to adopt the FPAS (Freezing and Packing for Seal) method. This is a method which combines packing which supports high water pressure and a freezing method, and ensures the maintenance of the stopped water state by sticking rubber blown up with air to the skin plate of the shield. This enabled construction to join the shield tunnel and submerged culverts with reinforced concrete in a state of water stoppage maintained for long periods of time under high water pressure (see Figure 4). At the time this method had only been used successfully once in the world and never before under such high water pressure conditions.
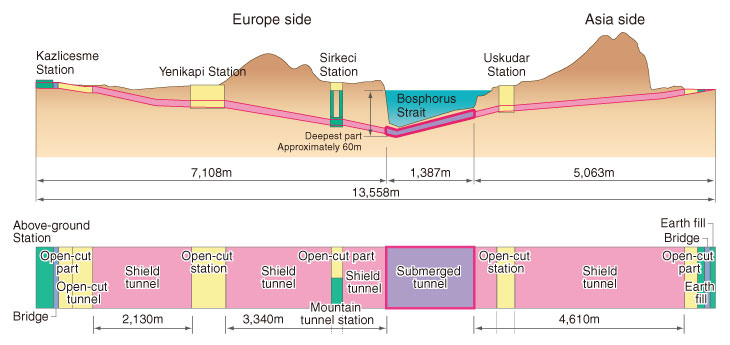
3.4Agreement Form Utilizing EPC (Engineers Procurement Construction)
The implementation via an EPC (Engineering Procurement Construction, a form where design, supply, and construction are implemented comprehensively) agreement can be highlighted as a characteristic which differs from the technological side. EPC agreements are normally applied where the construction risk is foreseeable in advance such as power plants constructed above ground, and would not essentially fit with this project where the construction is mainly underground. However, because the owner placed the order as an EPC agreement, the contractor had various obligations imposed upon it, such as fluctuating astronomical, hydrological, and ground condition risks, design liability, and equipment and quality assurance.
It was determined that the contractor would bear these risks and responsibilities, but the text of the agreement included clear and unclear things, so it was predicted that some differences of recognition and understanding between the parties would arise. Therefore, although the agreement form placed most of the risks upon the contractor, in order to arbitrate various agreement disputes and emergencies fairly a dispute arbitration committee was established. This committee consisted of one chairperson and 2 members for a total of 3 people, and their decisions were contractually effective. It was also possible to make notification of objection to the decisions of the committee and petition for mediation to the ICC (International Chamber of Commerce).
This project is still currently under construction, and at this point about 50 matters of dispute have been brought to the dispute arbitration committee. Examples such as construction period extension and costs caused by the historic ruins survey delay, responsibility for measures to handle frail buildings, and indirect expenses of design change construction were brought forward and resolved.
4Learned Lessons
Using the trans-strait railway constructed in this project, the time required to move across the strait has been dramatically reduced from about 30 minutes to 4 minutes. The Turkish government's decision to utilize the yen loan for this national project may have been because of the pro-Japan national sentiment stemming from the Ertug˘rul frigate disaster or their faith in the Japanese companies which had completed the construction of the No. 2 Bosphorus Bridge. As a result, the Japanese government granted a total of 153.2 billion yen loans for this project, which was the largest scale loan for a single project.
It was extremely difficult construction in a harsh environment, and although the construction period was extended to deal with the buried cultural property, the project is nearing completion with the efforts of Japanese engineers. On September 29, 2013, a ceremony for the formal partial opening was held to coincide with the 90th anniversary of the founding of the Republic of Turkey, and the Turkish people's long-sought dream of crossing the Bosphorus has finally been achieved. This ceremony attracted heavy attention from both countries with attendance by Prime Minister Erdog˘an and President Abdullah Gül from Turkey and Prime Minister Shinzo Abe from Japan, proving that it was a symbolic project for both countries.
This project would have been technologically difficult even if undertaken in Japan, so the engineers in charge of major design and construction were those who had many years of work experience in Japan, but their experience overseas essentially non-existent. On unfamiliar foreign soil they worked to communicate with people who possessed different cultures and backgrounds while creating technological solutions to lead to the success of the project, which resulted in the technological ability of Japan being widely transmitted to the world.
It must also be remembered that there was support from the Japanese embassy in Turkey and the Japan International Cooperation Agency as well as advice from university professors regarding the various execution methods. Industry, academia and government came together in this project to work for the export of Japan's technology while also deepening the friendly relations between the two countries, forming a new bridge between Turkey and Japan following the No. 2 Bosphorus Bridge.
Biography
Hidemi Ohmi
Taisei Corporation International Branch Advisor
Joined Taisei Corporation in 1970. Worked on public works technology development, various projects, general management of public works projects, etc.
As major project he experienced the construction of the national oil reserve bases in Kamigoto, Shibushi, and Hakushima.
He participated in this project from 2006 to 2012 as a representative of the joint venture and from 2013 to 2014 as the director.
Takashi Imaishi
Taisei Corporation International Branch Public Works Chief (in Charge of Construction) and Safety/Technology Promotion Department Chief
Joined Taisei Corporation in 1981. Worked mainly on the execution of shield construction.
As major projects, he headed the construction of the large section shield construction of the Tokyo Bay Aqua Line (Φ 14m), the Metropolitan Area Outer Underground Discharge Channel (Φ 12m), and the Loop Road No. 7 Kandagawa Underground Retention Basin (Φ 13m). After being the technology center public works technology development chief, he took up his current position from January 2014.
In this project he was the shield tunnel chief in the workshop from 2005 to 2010.
Masahiko Tsuchiya
Taisei Corporation Public Works Headquarters Public Works Design Department Chief (in Charge of Design) and Design Plan Chief
Joined Taisei Corporation in 1981. Worked mainly on planning public works structures.
As major projects he experienced the construction of the Metropolitan Expressway Kawasaki Route submerged tunnel, Tokyo Metropolitan Coastal Road submerged tunnel, etc.
In this project he was the design chief in the workshop from 2004 to 2011.